Service objectives
The following list represents the Key Service Objectives (KSO) for the Appleton Greene Process Excellence service.
Systems Overview
No business process operates in a vacuum, nor does any business system. Before any work on Process Excellence can be undertaken is it important to gather a detailed understanding of the business environment in which all processes operate. This is fundamental to process excellence. This will indicate key suppliers and customers as well as alternative or additional business streams. Additionally, critical “support” processes will be identified, which may contribute to new solutions. A systems approach will indicate key feedback loops within the system which need to be observed or which may contribute as inputs to problem processes. It is often a surprise for senior managers to work together to see their organisation mapped. It often leads to a clarity of understanding as to what the key and core processes are. Such an approach will identify the “golden thread” which must run through all processes in order to fulfil the organisation’s objectives. It also identifies initial areas of concern or excellence which can be used to commence work on. Before this mapping is completed process Reviews for all process may be carried out, unless it is very clear which processes need to be improved. An important output of this stage is an agreement on the processes to be improved, and the selection of key staff who will be involved in the process. This will allow for a detailed analysis of training needs and current skills of those who may be involved in the project. In addition, it is important to ensure that this initiative is communicated across the organisation. Such communication may be through large “conference” type meetings, but are better managed through small workshop groups across the company. It is important that everyone in the company is given the opportunity to embrace the initiative.
Process Reviews
The Process for improvement may come from any area of the company; ideally, but not solely, multi-functional processes have the best value in process excellence initiatives. (Thus an issue with cash collection may cover finance, sales, and order processing.) The details shown below apply to all processes which are selected for improvement. Having identified the processes for improvement, and reviewed the skills matrices, the potential team members are gathered together for workshops to explain the methodology that will take place. In particular, the importance and use of PDCA will be discussed with the teams. The group will first be facilitated in understanding the current process from inputs to outputs and production of the one paged summary document (SIPOC). In order to understand how each process operates currently the team will together produce detailed flow charts of the process, highlighting areas of concern to address, and of excellence to build upon. Further understanding as to how the process runs today will be gained by looking at data for current performance. If this does not exist in the appropriate format, it may need to be gathered again as the process run, which can be in itself a useful exercise. Having gathered the data the teams are taught to and then analyse the data. The analysis primarily concerns Statistical Process Control (SPC), and may be done using software (Baseline, WinChart and Minitab) depending on the Clients current and future needs. At this early stage it is useful for some sort of Visual Management to be introduced by each team. (These would include team details, up to date performance data recorded in SPC charts and any other information useful to outsiders). These serve as useful places for regular meetings about process performance. The process reviews of the as-is processes are summarised onto one page documents, showing key process steps, areas of concern and excellence, and customer needs and expectations. These are submitted to the senior management for review and comparison with the initial systems map.
Appleton Greene & Co Global – Successful change and process excellence should be built on existing strengths within the organisation. For this reason, Strength based change methodologies are applied; these allow the organisation to build on and appreciate what it has and continues to do well. In doing this change is seen in a positive light, and the adverse effects of “deficit” based change are avoided. A key element in the process improvement is the selection of key players within the organisation who can be used to encourage and drive the initiative. In this context they become “change leaders”. They will work as team leaders; process based teams will be heavily involved in the change process, in order that the initiative is accepted and embrace the changes making it “theirs”.
Process Transformation
This step takes place after each team have completed the Process Review for their process. Thus this may be running at different times throughout the organisation for differing processes. Building on the work completed so far, the team needs to understand what is causing the variation in the process, and, if unacceptable, what can be done to improve it. Some of these improvements may come from the initial flow charts, but it is important to ensure that no changes are made to processes without an understanding of the expected results of the change. The data then coming from the process is checked to see if these expectations have been met, and if not, why not. This stage involves imparting skills in analysing data, and in developing new theories. These methods will be taught to teams at this stage (Lateral Thinking and TRIZ). Distinction is made between “quick wins” and “longer term solutions”; the difference being defined by the organisation, but essentially seeking that quick wins are low cost, easy to implement and reversible. Throughout this stage data will be collected from the process and monitored in SPC charts, and displayed on the Visual Management boards. A key aspect of these charts is the ability that operational staff have to monitor the process themselves, and to act to keep the process in control.
Standardise Process
Once a process has been improved and is meeting the levels required for it, it is necessary for the improvement team to prepare to withdraw. This is done by standardising the process in its current form. The improvement team will document in high quality how the process runs today. It should also define the terms under which changes to the process may be made, if any; In particular it should address in detail how often data is to be recorded and monitored, and the actions for the operating teams to take in case the process ceases to be “in control”. The initial one page document produced by the team should be updated by the team to reflect the current reality, and should be displayed prominently on the visual management board. As the process is handed over the role of the Visual Management Board is increased, as it will show any actions taken to address out of control situations in the process; it continues to be a useful aid to senior managers who walk from process to process. It is therefore important that this board is kept live and managers involve themselves to ensure it is used and up to date.
Consultancy
In my time in consulting there has been a large shift from working for clients to working with clients. Given the prices paid, clients wish to gain more than the immediate work, and hope to be enabled to drive change themselves. Traditional consultancy seeks to recommend to management how the production staff should be treated to maximise output and efficiency. This traditional approach to consulting, as evidenced by companies such as McKinsey, suggests management to implement new policies and procedures. This is typically handled by the individual who carried out the study. In more recent years there has been a negative reaction to this approach, and a desire for a more “holistic” methodology in which the full system is understood, and buy in for all stakeholders is sought. This is seen as more sustainable; writers such as Peter Block and Peter Drucker have advocated such methods. Indeed Peter Drucker himself was a master of diagnosis and prognosis, typified by the ability to ask penetrating and challenging questions. The Consultancy sector appears to be struggling from its own past; many are critical or at best cynical of consultants, seeing limited value in paying high costs what they could do for themselves. With the internet many techniques and methods are available at no cost. Despite this banks and investors still rely on the work of the large consulting companies when carrying out Due Diligence exercises, or addressing concerns they have within businesses. One key attraction is the close link that such Consultancies have to accounting and legal professionals. However, there are those who realise the need for an outsider to facilitate consulting investigations. This has led to the growth of smaller consultancies, whose aim is to leave the company with more skills in it then when they arrived. Despite modern technology allowing remote working Consultancy continues to be preferred as requiring a personal approach. Certainly, to gain a good understanding of a business without visiting in person is difficult, if not impossible. Success in Consultancy is very much dependent upon building trustful relationships. This requires the consultant to have a good basis of knowledge upon which this trust can be built. Because of the move away from large Consultancies, and the rise in unemployment amongst skilled professionals, there has been a growth in the number of small consultants; in the UK in 2014 there were 80,000 consultants. The future should allow smaller consultants to gain access where in the past the larger companies have been prevalent; there is a greater willingness from smaller consultants to challenge the clients of what the “need” and to enter into discussion as to what is better for them. Much of this is driven by the need to use more personal and intimate techniques such as appreciative inquiry. With more older and experienced people available, consultancy can and should be able to offer a vast amount of skill and knowledge to clients, which would otherwise be wasted.
Manufacturing
Manufacturing world-wide, is influenced by developments in technology. In research and design, cloud based technology is having a considerable impact, allowing design to be offshored, particularly to design centres, such as India. In operations, smaller pcs, and tablet based technology are finding their way into the production process. This is really a mixed blessing. The ability to gather considerable amounts of data, can lead to more confusion at the workface than to solving problems. One Process Engineering company where I worked as a consultant, where able to measure the thickness of materials on a conveyor belt system on which material was transported. Sensors were able to measure the thickness of the material at 100 points across its width, every second. The width of the material did not exceed 2 metres. Whilst measurement across the width was important to the process, the system which showed these 100 measurements every second was intelligible; my recommendation was to take sample readings both across the width and in time, to eliminate the “noise” from the data. When this suggestion was accepted it allowed for a much clearer analysis of the data to immediately highlight problems in the process. In production processes, robotics are increasingly more important. These are often introduced as part of lean manufacturing, as the time they take to complete most tasks in relatively stable, and thus the flow through the process easy to calculate and monitor. With robotic automation the use of “fail safe” technologies is increasing important, with “Andon” methods to warn of problems and to shut the production line down. This had meant the human operators are not excluded from the process, with one person being responsible for a number of robotic or automatic (such as CNC machines) machine cells. Thus today the challenge must be to use technology correctly, and to continue to engage people as experts in the process. Virtual teams are increasingly more important, with managers often taking responsibility for a number of plants across the world. My work in manufacturing has increasingly involved new statistical methodologies such as design of experiments. The pressure from Far East producers is likely to intensify. China, Taiwan and Vietnam are likely to become more competitive. Japan is not likely to lose its place in the production of Electronic goods and in the automotive sector. The development of new manufacturing countries in the automotive industry, particularly in the old eastern Europe, such as Skoda as an offshoot of VW, and Hyundai, now the 5th largest auto manufacturer, and established initially by Ford in Korea, is likely to be reflected in other industries. Both Automotive and Aerospace a pushing the long awaited move away from specification, to the adoption of true world class quality, “on target with minimum variation”. In order to compete in a global market western manufacturers will need to become more efficient. This does not require large investments, but requires culture changes to all the organisation to embrace both continual improvement and lean methodologies.
Non-Profit & Charities
The not for profit sector is wide, covering charitable foundations to government departments and non-governmental organisations, as well as religious foundations. In the UK, the most recognisable not for profit organisation is the National Health Service (NHS). Founded by the Labour Health Secretary Aneurin Bevan in 1948, with the aim of providing good health care to call, free at the point of service. The common ground is that all money earned or generated is used to accomplish the organisations objectives. The NHS objective of “free at the point of service” typifies many UK not for profit organisations, such as the Citizens Advice Bureau, Samaritans, RSPCA, RNLI, RNIB. The writers’ experience of delivering change within the NHS is of staff who are desperate to see change, led by managers driven by counter-productive targets. Recently there has been a growth in the Charity sector, but government not for profit organisations are struggling with financing and in balancing their budgets. In the UK the NHS is under extreme pressure. In schools, new solutions for funding and excellence have been sought. With the demise of Grammar Schools, “Academies” are the new “solution” for providing high level education. These could well indicate the new direction being taken, which is local management and local responsibility. Much activity within not for profit organisations (such as “Business Wales” is led from a devolved situation) Thus in not for profit, devolution is the rule, rather than centralisation. The not for profit sector is unlikely to see any reduction in activity; on the contrary increased activity is likely. For the reasons that this sector grew, lack of government or private funding, growth is probable. In specialist areas such as health or education barriers to entry still exist, and without specific experience of these areas it is hard to gain access. Additional ways of giving donations, and tax benefits of doing so would assist the sector; the development of social media (Facebook) and modern technology may allow the organisations to become better known, and their activities more widely publicised. Against this, increasing impatience of the public with cold calls and what is seen as harassment, will require the organisations to be more discrete in their collection activities. As was discussed earlier, the sector depends largely on independent and localised staff, many of whom may be volunteers. This independence is likely to come under pressure as both governments and private sector seek to gain influence by buying their way in. The sector is likely to be squeezed between the pressures of governmental and commerce in the one hand and volunteers with social agendae on the other. This may lead to increased accountability; certainly large corporate donors may require this. The sector will see continued growth; success will be determined by the ability to manage this growth while driving efficiency and effectiveness without increasing resources. Thus the sector is in need of more advice on driving excellence and achieving quality.
Food & Beverage
Many larger companies in this sector have developed from manufacturers and by embracing agriculture where able to control the full supply chain of agricultural product. Outside the alcohol sector, the industry is strongly influenced by health foods, as well as by the frozen goods market. The sector covers the whole product life cycle. In Beverages, the sector may be divided between alcoholic and non-alcoholic. In terms of development of the sector non-alcoholic it must be seen as the area where development took place. Led particularly by Coca-Cola methods for production of extremely large quantities of bottled produce were devised. The sector must also take the credit for the development of packaging in terms of tins and Cans, and more recent PET, which had cross-overs into another sector, that of man-made fibres in clothing. The development of branding and marketing was much influenced by this sector, in the drive to distinguish similar products which were essentially the same; (examples of this might be Coca-Cola vs Pepsi or differing Beers against each other). Both sectors within the main sector are working against current trends; the efforts of governments to reduce both alcohol and sugar intakes, is leading to more transparent packaging and changed marketing tactics. The sector is being forced to appear socially responsible and not to encourage obesity or addiction. The latter is also a concern the alcoholic sector of the beverage industry, which is having to stop catering for younger drinkers with such things as “Alco-pops”. At the front end of the sector traditional resellers are being challenged by new entrants who have wider foot prints and are thus able to command lower prices and able to sell cheaper. In the UK Asda has been acquired by Walmart, whilst two German entrants, Lidl and Aldi are taking over from traditional Grocery resellers, who appear to be at a loss how to respond. With food quality becoming a key concern, it is likely that this sector will become increasingly subject to government legislation. In the USA the FDA (Food & Drug Administration) is already becoming active in requiring Food Safety Incident reports. In the UK, it is likely that the FDA’s example will be followed, as it has in the Pharmaceutical Industry. As in that industry FDA regulations have become standard and accepted across Europe; one can expect the same to apply in the handling of food and drinks where quality and safety are paramount. Given a current resistance to Genetically Modified Foods, and the pressure for Organic products, this is likely to continue in the future. The increased concern about Carbon Foot prints will add to the pressure for locally made products. The sectors will not see significant downturns; vitamin fortified waters, and energy drinks will continue to fuel the need for new products. The future will be based on strong marketing and on efficient and effective production processes.
Pharamaceuticals
The USA’s FDA has a strong role to play in pharmaceutical safety across the world. With concerns about product safety rising, and less risk adverse regulation, a more recent issue to arise has been that of animal testing. Although unpopular, some producers continue to use animals to test products. Many argue this testing is necessary before permitting testing on humans. It is therefore highly regulated in itself. Companies which practice it are subject to much abuse, with damage to their premises often being inflicted by animals’ rights campaigners. Testing before production and after remain a challenge. Clinical trials are controlled aggressively, meaning costs are higher. In production tests are carried out at each stage of the production line, (to produce traceability in much the same way as the aero industry). If these tests do not give satisfactory results every batch will be condemned and not available for sale. Given the very high costs of some components, this is a concern, and requires producers to have world class production facilities. Costs of medications need to be controlled. Pharmaceutical companies have high R&D costs and need to recoup these fast. Success comes by bringing new drugs to the market. The problem lies in that what has not yet been developed is complicated to manufacture safely. With the pressure to reduce resale costs the challenge is how to recoup these costs. A current issue surrounds the production of cheaper and more generic drugs. In response to medical authorities refusing to spend on more expensive drugs cheap suppliers have set up in offshore locations, such as India. Organisations such as MSF have benefited considerably from these cheaper drugs, particularly in treating widespread illnesses such as HIV/AIDS. Medical professionals are under pressure not to use more expensive treatments. The current situation is thus marked by high costs and low product prices, with increasingly strong regulation. Competition comes from unregulated sources, who have copied generic formulae and are able to sell cheaply. The issue of Indian manufacturer of generic drugs is currently being addressed by the EU, who seek to require these producers to follow international standards and to abide by patents. Increased age expectations, chronic diseases are increasing; notably “new killer diseases” such a Alzheimer’s, requiring increased research, but against this the costs of medications are being driven down by health authorities. The authorities will increasingly determine the exact nature of the drugs which can be prescribed. Future medications must have very clear and deliverable benefits. Alternative strategies could be in collaborations between larger companies, possibly ending in mergers / acquisitions, and improved manufacturing processes which adhere to FDA guidelines. There is a trend towards prevention rather than cure. This is exemplified in the area of alternative (natural) treatments, which is an area that the sector will need to watch closely. In the same way that some large companies (Virgin; Hilton) have become synonymous with heath care (in its wider sense or fitness), this may be a route that the large Pharma’s will follow.
Bronze Service
Monthly cost: USD $1,000.00
Time limit: 5 hours per month
Contract period: 12 months
Bronze service includes:
01. Email support
02. Telephone support
03. Questions & answers
04. Professional advice
05. Communication management
SERVICE DESCRIPTION
The Bronze Client Service (BCS) for Process Excellence provides clients with an entry level option and enables client contacts to become personally acquainted with Mr. Boland over a sustainable period of time. We suggest that clients allocate up to a maximum of 5 Key Employees for this service. Your Key Employees can then contact the consultant via email, whenever they feel that they need specific advice or support in relation to the consultant’s specialist subject. The consultant will also be proactive about opening and maintaining communications with your Key Employees. Your Key Employees can list and number any questions that they would like to ask and they will then receive specific answers to each and every query that they may have. Your Key Employees can then retain these communications on file for future reference. General support inquiries will usually receive replies within 48 hours, but please allow a period of up to 10 business days during busy periods. The Bronze Client Service (BCS) enables your Key Employees to get to know their designated Appleton Greene consultant and to benefit from the consultant’s specialist skills, knowledge and experience.
Gold Service
Monthly cost: USD $3,000.00
Time limit: 15 hours per month
Contract period: 12 months
Bronze/Silver service plus
01. Management interviews
02. Evaluation and assessment
03. Performance improvement
04. Business process improvement
05. Management training
SERVICE DESCRIPTION
The Gold Client Service (GCS) for Process Excellence is intended for more detailed evaluation and assessment, that may require your Key Employees to have monthly meetings or interviews with Mr. Boland. These meetings and interviews can be conducted over the telephone, Skype, or by video conference if required. The consultant can also attend your business premises, an Appleton Greene office, or another mutually beneficial location, but please note that clients are responsible for the costs of any disbursements separately, including travel and accommodation. This service enables you to integrate the specific skills, knowledge and experience of your designated consultant into your Key Employee management team. The Gold Client Service (GCS) can also incorporate training workshops, business presentations and external meetings with customers, suppliers, associations, or any other business-related stakeholders.
Platinum Service
Monthly cost: USD $4,000.00
Time limit: 20 hours per month
Contract period: 12 months
Bronze/Silver/Gold service plus
01. Project planning
02. Project development
03. Project implementation
04. Project management
05. Project review
SERVICE DESCRIPTION
The Platinum Client Service (PCS) for Process Excellence is our flagship service and will be required if you need Mr. Boland to facilitate the planning, development, implementation, management, or review of a particular project relating to his specialist subject, which would obviously require more time and dedication. This service enables you to reserve up to 12.5% of the consultant’s working month and provides a more hands-on service as and when required. If you need more time than this, then this can always be arranged, subject of course to the consultant’s ongoing availability. The benefit of having an external consultant involved in projects is they provide an independent perspective and are not influenced by internal politics, day-to-day responsibilities, or personal career interest. They provide objectivity, specific knowledge, skills and experience and will be entirely focused upon the tasks at hand. The Platinum Client Service (PCS) will provide your organization with a valuable resource as and when you need it.
Benefits
Management
- Skilled staff
- Improved results
- Continual improvement
- Learning organisation
- Team work
- Clear strategy
- Motivated staff
- Shared vision
- Reduced complexity
- System understanding
Customer Service
- Delighted customers
- Improved relationships
- High quality
- Committed teams
- Improved satisfaction
- Less complaints
- Market reputation
- New customers
- Faster processes
- Market responsiveness
Finance
- Reduced costs
- Less waste
- Transparent data
- Faster data
- Integrated organisation
- Working capital
- Fast close
- Reduced documentation
- Cash flow
- Less complexity
Clients
This service’s current clients or employers include:

A.Friedr Flender AG
This company, was acquired by Siemens in 2005, and is now part of their automation and drives division. Because of this I quote from an old Bloomberg description of the company: “A. Friedr. Flender AG manufactures mechanical power transmission equipment and components. It offers standard gear units for drive systems such as gear units, SIG, planetary gear units, and SIP for the field of mechanical power transmission technology; custom-made gear units; and supplies, including bevel gear sets. The company also provides application-specific gear units for aerators, agitators, air cooled condensers, belt conveyors, bucket elevators, bucket wheel excavators, cranes, crushers, extruders, jack-up rigs, lauter tuns, paper and pulp preparation sections for railway vehicles, reactors, roller presses, ropeways, rotary kilns, ships, sugar mills, tube mills, vertical mills, water screw pumps, water turbines, and wet cooling towers. In addition, it offers field service inspection and maintenance, repair, condition monitoring/condition diagnostics, and gear unit modifications; and spare parts and spare gear units. The company was founded in 1899 and is based in Bocholt, Germany. With around 36,000 employees worldwide (September 30), Siemens Drive Technologies achieved total sales of €7.5 billion in fiscal year 2009.” In the drive technology sector, the product name FLENDER has a special ring to it all around the world. That is, of course, not only a result of the unparalleled reliability of our products. During over 80 years as a manufacturer of gear units, we have built up extensive industry know-how that has contributed to the quality of our products and solutions over the decades. Customer relationships have evolved into development partnerships, special assignments have resulted in exceptional solutions and innumerable customer-specific gear units have led to comprehensive modular systems that offer unlimited possibilities. With every drive application for which we provide the solution, we continue to expand our expertise in other applications as well. In the drive technology sector, the product name FLENDER has a special ring to it all around the world. That is, of course, not only a result of the unparalleled reliability of our products. During over 80 years as a manufacturer of gear units, we have built up extensive industry know-how that has contributed to the quality of our products and solutions over the decades. Customer relationships have evolved into development partnerships, special assignments have resulted in exceptional solutions and innumerable customer-specific gear units have led to comprehensive modular systems that offer unlimited possibilities. With every drive application for which we provide the solution, we continue to expand our expertise in other applications as well.
A.Friedr Flender AG – Click Here
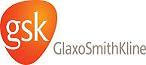
Glaxo Smith Kline
GSK is science-led global healthcare company on a mission: is seeks to help people do more, feel better, live longer. GSK want to change that there are still millions of people without access to basic healthcare, thousands of diseases without adequate treatments and millions more people who suffer from everyday ailments. GSK have three world-leading businesses that research, develop and manufacture innovative pharmaceutical medicines, vaccines and consumer healthcare products. GSK is committed to widening access to our products, so more people can benefit, no matter where they live in the world or what they can afford to pay. GSK, as a global healthcare company, takes on some of the world’s biggest healthcare challenges. By delivering a sustainable business, GSK provides health benefits to patients and consumers, improved shareholder returns as well as supporting wider society. Each GSK three businesses benefits from GSK’s commercial infrastructure, integrated supply networks and significant global presence. The mission is to help people do more, feel better and live longer. The business is focused around the delivery of three strategic priorities which aim to increase growth, reduce risk and improve our long-term financial performance. These priorities are: grow a balanced global business, deliver more products of value, and simplify the operating model. Operating responsibly and ensuring GSK values are embedded in our culture and decision-making helps us better meet the expectations of society. Grow a balanced business. GSK has been creating a more balanced business and product portfolio, capable of delivering sustainable sales and earnings growth and improved returns to shareholders. This is centred on three business areas of Pharmaceuticals, Vaccines and Consumer Healthcare.
Glaxo Smith Kline – Click Here
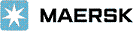
Maersk Group
The Maersk Group is a worldwide conglomerate and operates in some 130 countries with a workforce of over 89,000 employees. In addition to owning one of the world’s largest shipping companies, Maersk is involved in a wide range of activities in the shipping, logistics, and the oil and gas industries. The Maersk Group has five core businesses which include Maersk Line, APM Terminals, Maersk Oil, Maersk Drilling and APM Shipping Services. The last business area is comprised of Maersk Supply Service, Maersk Tankers, Damco and Svitzer. Maersk Line is the world’s largest container shipping company, known for reliable, flexible and eco-efficient services. We provide ocean transportation in all parts of the world. We serve our customers through 374 offices in 116 countries. We employ 7,100 seafarers and 25,500 land-based employees and operate 608 container vessels. Interesting facts: Total value of goods transported estimated at USD 675bn in 2012; Ocean transport costs from Asia to Europe (2012 In USD): A flat-screen TV $4, a pair of sport shoes 22 cents, a T-shirt 8 cents, and a tablet 10 cents; The Triple-E vessels can hold 18,000 twenty-foot containers; In November 2014, Maersk Line announced an ambitious CO2 target to reduce 60% in emissions per container by 2020 (2007 baseline). We reached the previous target of 40% in 2014; In Q1/2015, Maersk Line’s total bunker (fuel used by ships) consumption was 1.8% higher than Q1/2014 as a result of lower utilization.
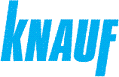
Knauf Group
Knauf, a family name, and a corporate group of global dimensions. At the same time synonymous with a type of corporate culture which has become rare. Knauf is a typical family firm in spite of its size and this is precisely the reason for its amazing success. It is the short and direct decision-making paths, the courage to tackle new ideas, innovations, investments and the wealth of ideas contributed by all Knauf employees that characterises the company. Knauf was founded in 1932 by the brothers Karl and Dr. Alfons N. Knauf. Today their sons, managing partners Baldwin and Nikolaus Knauf, steer the success of the corporations’ numerous enterprises in close co-ordination with the other family members. From its beginnings in gypsum processing along the Saar and Main rivers, Knauf has expanded and diversified to become a corporation with worldwide activities, delivering products and services in the following fields: Building materials and systems based on gypsum and gypsum-related products; Thermal insulation and sound insulation materials; Limestone and lime products; Chalk and cement related products and Plant engineering. Besides Knauf Insulation, Knauf also operates Knauf Drywall and Knauf Marmorit in the UK: Knauf Drywall – Plasterboard & Drylining Systems and Knauf Marmorit – solutions for ‘external wall insulation’ and ‘render’ applications. Knauf Insulation is the UK’s leading insulation company. It represents one of the most respected and progressive names in European building products. Formed in 1946 as Fibreglass Insulation it has been previously known as Pilkington Insulation and Owens Corning before the involvement of Knauf with KnaufAlcopor before finally becoming known as Knauf Insulation. Knauf Insulation is active in more than 35 countries with 40 manufacturing plants and over 5,500 employees across the globe. The company, which is part of the German family-owned Knauf Group, continues its strong and steady operational and financial growth, having achieved a turnover well in excess of € 1.4 billion in 2014. Knauf Insulation is the only UK manufacturer of glass mineral wool, rock mineral wool and extruded polystyrene insulation products, giving an unrivalled range for building, H&V, process and appliance insulation, as well as fabrication applications.
Process Management International Ltd
Our process and improvement services enable clients to achieve unprecedented results. Transform your goals into results with us. The difference with PMI’s BPM is our systemic approach. We help you understand your organisation as a system rather than a series of functional processes. This enables performance improvements to be made in context rather than in isolation which is critical to achieving optimum outcomes. Whether you are concerned about process owners, process capability, process improvement, process managers or pretty much anything else to do with BPM (!), we can help. Achieve your full potential with our unique approach to coaching that embraces the value of transformation – for you and your organisation. Understand your strengths, how to use them and understand how others see them. We have developed a broad consulting capability covering the many facets of improvement. Our message is simple: using our powerful methods, capable people and expertise in all things process, we can help you transform your goals into results. In order to understand your direction of travel, it is hugely important to understand where you are starting from. This is where our Business Process Assessment and review can help. PMI can provide interim operational excellence managers at short notice for any period of time, anywhere in the world. And you can get on with running your business.
Process Management International Ltd – Click Here
Locations
This service is primarily available within the following locations:
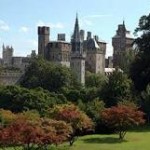
Cardiff UK
Cardiff is a vibrant city, home for many large companies in many sectors; including Financial Services, Food, and Manufacturing. Manufacturing continues to develop North of Cardiff in the important valleys area, prestigious names being headquarter there; Aston Martin and TVR. Cardiff is the most densely populated area in the whole of Wales with around 11% of the population of Wales, seeing recent annual increases above that of Wales as a whole. Cardiff University, a campus of the University of Wales is around 30th in various rankings of UK universities; a member of the Russell Group of research-led universities, in 2014 it had two Nobel Laureates on its staff. It maintains close links with local business to provide a centre for research and development. The recently (1999) completed National Stadium, the “Millennium Stadium”, now the “Principality” Stadium, sponsored by a local Financial Services company, is a state of the art Stadium used for sporting and music events. With a capacity of 75.000 it is the second largest stadium in the world having a retractable roof. Now refurbished, Central Station sees 12 million passengers each year, serving as a hub both west to ferry Routes to Ireland and East to London and the rest of the UK. Together, the Millennium Centre, a large multi-halled arts centre and the St David’s Shopping Centre, only the 11th largest in the UK, but in the top two in the UK for visitors, attract many visitors. The development of Cardiff Bay Barrier scheme, with subsequent growth of the Waterside area, the largest Waterside development in Europe, has significant impact on Cardiff, making it both an attractive City to live and work in, attracting visitors and new income. In 2016 Cardiff was joint 3rd in best Cities in Europe, with Stockholm and Copenhagen. Cardiff was founded on excellent and developing transport links; as will be its future. Cardiff is in the top 10 in the UK for population growth, fast broadband access and growth in homes built. This growth is predicted to continue in the future. While Wales is considerably influenced by UK general trends, Cardiff provides the heartbeat for Wales, and the focus is on the city to ensure that it continues to drive through growth. In line with this, Electrification of the Valleys railways by 2017, and the lines west to Fishguard and Milford Haven, will support future growth. Some concerns of the “Brexit” decision, as Wales previously enjoyed considerable EU financial funding, are resolved; as the UK government will replace this at least until 2020. The region possesses workers skilled in manufacturing; the move of Aston Martin and TVR to the area shows the opportunities for continued inward investment. Recent growth in Financial Services in Cardiff adds skills to the local working population for incoming companies. The vision for the future is stated in the 2010-2020 strategic plan, much of which has already been completed. Infrastructure development is still underway, particularly electrification of the surrounding rail network, and improvements to local motorway network.
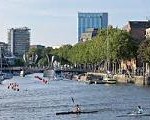
Bristol UK
Built on a significant industrial history, and powered by the early development of rail and shipping routes, Bristol grew with a divergency of industries, which continues today. Bristol remains a vibrant and active City. Essential to its status today as an administration centre for financial services. Its Central Station, Temple Meads, a link with Bristol’s past, was designed and built by Brunel in 1841. As in the past, Bristol is home to a divergent range of Industries; ranging from IT, which is increasing in the City, Heavy Industry, with Babcock and Airbus having large operations there; Financial Services , Transport and Distribution. Unemployment in the City is slightly below the national average. In 2008 Bristol was named as the UK’s first cycling city, followed in 2013 with it being placed in the top 10 of world cities for being bicycle friendly. This, together with excellent local and national bus and train routes makes the City easy to both live and work in. Whilst its central station, Temple-Mead’s offers good national connections, the northerly station on the busy London to Wales and the West motorway system, Bristol Parkway, provides easy commuting to and from Bristol across the City. Bristol has an airport, which serves national and international routes. It is serviced by large national and international discount and premium carriers. Thus Bristol has excellent travel links within and outside the UK. Served with two first class universities, Bristol attracts high level students across many disciplines; this will serve its future well, as good universities will attract good employers. With its excellent transport links to the whole of the UK, Bristol is increasingly chosen as a head-office location for companies moving out of London. Bristol has set its target as developing a low Carbon future by 2050, with a number of plans in operation; in this it will become increasingly cycle friendly and will seek to attract and develop renewable energies.
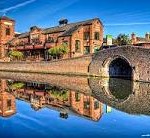
Birmingham UK
From a medieval market town, Birmingham developed in metalworking, leather and wool. With a number of natural advantages, which have driven its growth in the past; its location in the centre of England and its place in the middle of a growing network of medieval routes; nearby coal and iron deposits, and good waterways providing power for water mills. The growth in the canals, the development of rail across the UK impacted strongly on Birmingham. In the early 1900’s Birmingham became the centre of Car production in the UK, with a number of Private companies (Rover, Morris, Jaguar, Land Rover) merging to form the British Leyland Motor Company. Birmingham’s skill force in the industry has kept the industry in the area: Jaguar Land Rover have a large presence. In 2016 the world’s largest automotive supply chain trade show was held in Birmingham’s large Exhibition Centre the NEC. The venue, its location and the exhibition show the importance of Birmingham today. The NEC, opened in 1976 is the UK’s top venue, hosting more than 500 events a year, it is by far the largest in the UK, with ample parking and excellent transport routes. Birmingham has three world class universities and other tertiary colleges, attracting students from around the world. There is cultural diversity; more than 40% of its population is non-white, British or otherwise. Transport routes remain excellent, with road, rail and air routes to national and international destinations. Its International Airport, easily accessible from the city, is the UK’s seventh busiest airport, with over 9 million passengers a year, and now served by Emirates A380’s to the Middle East. Birmingham has a diverse list of top employers, ranging from Transport Services (National Express), Supermarket Head offices (Sainsbury’s), Food and Confectionery, Business and Financial Services, as well as automobile industry, and metal working industries. Business and Financial services and tourism are the more important industries. 256,000 people live and work in Birmingham, and around 300,000 in the Greater Birmingham area. 50% of the population of Birmingham are qualified at NVQ 3 and above; these statistics indicate a qualified and mobile workforce in the City. With an important place in the UK traffic system, and the UK’s largest exhibition centre, with a still thriving automobile industry the future for Birmingham should be bright. It has a mobile and qualified and skilled population. Concerns of the effect of “Brexit”, largely in the automotive sector; however, there is little reason why the city should not prosper with ties to the rest of the world. The population connections with India and the Middle East should provide a solid backdrop against which trade and expertise can be transferred to those areas. The key universities offer attractive study and research centres, supported by a regional policy to develop research and led by Aston University. Research thrives in medicine, engineering and life and health sciences; the diverse structure of the city’s industry should provide a good spring board for future growth and further diversification.
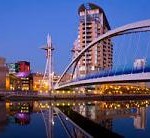
Manchester UK
Built on cotton and silk weaving, with transport links developed on the water ways and later rail, Manchester was the work place of innovators such as Arkwright, who patenting the spinning and carding machine, and was actively involved in improving the textile industry. However the early 1900’s brought a decline in the traditional industry of cotton, as well as engineering, with competition from Leeds and the Midlands. In the early 1900’s Rolls Royce started production of their cars in the City. More recent history is notable for the growth of “Chinatown” since the 1970’s; sadly an IRA bomb in 1996 caused damage to life and property in 1996, but this gave rise the Trafford Shopping Centre a large indoor shopping centre, the second largest in the UK, attracting more than 35 million visitors a year. Today Manchester is placed situated in the second most populated urban area in the UK; it has benefited considerably from recent improvements and developments is Salford Quays, which has become a major centre for the BBC, and the Trafford Shopping Centre which brings many visitors from around the area to the city. Manchester continues to have an important role in the arts, with a top orchestra, the Lowry art exhibition, ballet and opera. Traffic connections to Manchester are excellent, both nationally and internationally. As a key centre of the South/North rail link to Scotland it is in reach of all the UK by rail. Manchester Airport is the second largest after London; it has links both within and outside the UK; it has recently been named best UK airport. Work is currently underway on new traffic routes across Manchester, currently difficult to travel. As the best airport for the area covered by the M62 Corridor, it is the first choice for flights outside Europe. Manchester’s mixed ethnic population and excellent transport links, place it as a good location for companies moving out of London. With an already excellent industrial infrastructure it should continue to be an important centre not just in the UK, but also in Europe.
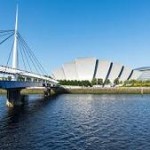
Glasgow UK
Glasgow’s development was built on it being a market town, where leather production and wool were its foundations. Being coastal there was naturally commerce in fish, but linen and cotton spinning became increasing important. Glasgow has thrived since it was named European City of Culture in 1990; it has good art collections, restaurants, is home to the Scottish Ballet, Opera and the Royal Scottish National Orchestra. It has two excellent universities, both of which have very high research involvement. Glasgow is the UK’s fourth largest City with 1.7 million people in the greater Glasgow area. It is in the top 30 largest cities in Europe. The work force is well educated, being second to London in the UK for level of graduates employed. The city has diversified industries, with a few sectors being significant; low carbon, financial and business services, life sciences, engineering, energy (particularly renewables) and education. Being a gateway to the highlights of Scotland tourism is important. 80% of the Whisky bottling for Scotland takes place in Glasgow. The future of Glasgow, more than many other UK cities, is troubled by uncertainties over Brexit. This is due to the high dependency on EU funding for the Universities, with many EU students there, and for research projects. Despite this the life sciences industry, hosting the Glasgow Bio-Corridor, and funded partially from GSK (a US company) should allow for continued growth and development. The Financial and Business services sector should also allow the city to continue growth. Today the city is 74th in the world ranking of financial centres; the sector employs 52,000 in large banks and institutions. This makes the private sector in Glasgow amongst the fastest growing in the UK. With a strong history in Engineering, and hosting many important engineering companies, (with around 10,000 professional engineers working in the City), supported by Universities with a strong engineering emphasis, there is no reason why Glasgow should not continue its growth based on a diverse but strong economy. The supply of talented staff can only be of benefit to the future. It is for the business leaders of the city to take these opportunities, and overcome the uncertainties that Brexit may have caused.
Testimonials

A.Friedr Flender AG
Mr Boland worked with remarkable success in his entrusted tasks and he contributed considerably to the success of the company in the last years. His personal conduct was faultless, as regards system and effort, and was marked with high timeliness. He was equally regarded by the Board, employees and colleagues, and fulfilled his responsibilities effectively and successfully, with a high degree of loyalty. He orientated his staff towards goals and success. He was an acknowledged partner and leader due to his technical knowledge and team guidance.
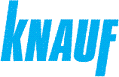
Knauf Insulation Ltd
Mr Boland has been heavily involved in our Process Excellence initiative from the start, providing invaluable support throughout. This support has been wide-ranging, covering many aspects from consultancy and advice for the management of the initiative across our pan-European businesses through to delivering training and advice to specific manufacturing, technical and engineering projects. The depth to which Mr Boland has embraced his role has meant that he has gained an exceptional level of knowledge our manufacturing processes. So much so that he has become an acknowledged source of technical and engineering advice – especially regarding optimisations specific to our processes. A rare combination for someone external to our organisation. I believe he would have been just as confident in running most of our processes as he would delivering any of his training subjects. His willingness to become involved and keenness to understand, combined with his already considerable multi-faceted experience is an invaluable asset to any company at any level – and I am more than happy recommending him in any of the above disciplines.
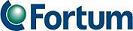
Fortum
Mr Boland is a great coach, trainer and a consultant. He works easily with top management all the way to first line employees. He has high ethics and has a high motivation in helping you with whatever questions you have regarding business and process improvement. I’ve worked with Mr Boland for a couple of years within the areas of business process management and lean six sigma. He was our company’s key trainer and coach. I can recommend Mr Boland to anyone interested in improving the skills and competences related to process improvement and lean six sigma!
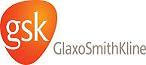
Glaxo Smith Klein
I’d recommend Mr Boland as a trainer from my Six Sigma Black Belt course. I enjoyed the training; Mr Boland was an engaging and knowledgeable presenter and I thoroughly enjoyed my time working with Mr Boland, his pragmatic open approach, and ability to convey some complex concepts simply.
Personal Profile
Mr Chicles is an approved Certified Learning Provider (CLP) at Appleton Greene who is a business leader and strategist with broad experience in the global multi-industrial, aerospace and defense sectors. He is a seasoned operational leader of global industrial businesses, leading transformational strategies in highly competitive markets.
As a senior, C-suite strategist for multiple major industrial corporations he has led multiple mergers, acquisitions, divestitures and restructurings, as well as corporate break-ups and spin-offs. He has a distinguished track record of successful transformations of complex organizations in dynamic and uncertain market conditions while engendering the trust and buy-in of employees, customers, vendors, owners, corporate leadership and boards of directors.
A highly engaged leader at the personal and team level he has demonstrated the ability to engender effective senior teams and boards. He’s also an active mentor, teacher and community leader.
Mr Chicles is an active board member with AES Seals, global leader in sustainable reliability engineering, and Micro Technologies Inc, an electronics and advanced manufacturing company. He is a principal partner with ProOrbis Enterprises®, a management science consultancy with premier clients such as the US Navy and PwC, as well as the principal of Xiphos Associates™, a management and M&A advisory. Recently, he served as Board Director and Chairman of Global Business Development with Hydro Inc. the largest independent pump and flow systems engineering services provider in the world.
He was President of ITT’s Industrial Process / Goulds Pumps business segment a global manufacturer of industrial pumps, valves, monitoring and control systems, and aftermarket services for numerous industries with $1.2 billion in revenue, 3,500 employees and 34 facilities in 17 countries. Preceding this role he served as Executive Vice President of ITT Corporation overseeing the creation of a newly conceived ITT Inc. following the break-up of the former ITT Corporation to establish its strategy and corporate functions such as HR, communications, IT and M&A, building the capabilities, policies and organizations for each.
He joined ITT Corporation’s executive committee as its strategy chief in 2006 and instituted disciplined strategic planning processes and developed robust acquisition pipelines to respond to rapidly changing markets. Created successful spin-offs of 2 new public corporations Exelis Inc. and Xylem Inc. ITT Corporation was named one of “America’s Most Respected Corporations” by Forbes for exemplary management and performance during his tenure there.
Before joining ITT, Mr Chicles served as Vice President of Corporate Business Development and head of mergers and acquisitions for American Standard / Trane Companies, where he initiated and closed numerous transactions and equity restructurings globally.
Additionally, he created and led the corporate real estate function which entailed more than 275 real estate transactions around the world.
He began his career at Owens Corning rising through the ranks in various operational roles to Vice President of Corporate Development.
Recently, he taught advanced enterprise strategy at Stevens Institute of Technology as an adjunct professor and still supports start-ups through the Stevens Venture Center. He continues to be active as the Founding Board Member with several successful start-up technology businesses and non-profit organizations. A community leader, Mr Chicles has held the role of President of the Greek Orthodox Cathedral in Tenafly, N.J., He also led trips abroad to Cambodia and Costa Rica to build sustainable clean-water solutions and affordable housing.
His formal education includes earning a Masters of Business Administration from The Wharton School at the University of Pennsylvania, and a Bachelors in Finance from Miami University.
(CLP) Programs
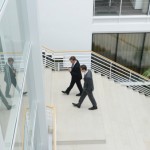
Appleton Greene corporate training programs are all process-driven. They are used as vehicles to implement tangible business processes within clients’ organizations, together with training, support and facilitation during the use of these processes. Corporate training programs are therefore implemented over a sustainable period of time, that is to say, between 1 year (incorporating 12 monthly workshops), and 4 years (incorporating 48 monthly workshops). Your program information guide will specify how long each program takes to complete. Each monthly workshop takes 6 hours to implement and can be undertaken either on the client’s premises, an Appleton Greene serviced office, or online via the internet. This enables clients to implement each part of their business process, before moving onto the next stage of the program and enables employees to plan their study time around their current work commitments. The result is far greater program benefit, over a more sustainable period of time and a significantly improved return on investment.
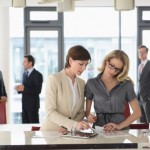
Appleton Greene uses standard and bespoke corporate training programs as vessels to transfer business process improvement knowledge into the heart of our clients’ organizations. Each individual program focuses upon the implementation of a specific business process, which enables clients to easily quantify their return on investment. There are hundreds of established Appleton Greene corporate training products now available to clients within customer services, e-business, finance, globalization, human resources, information technology, legal, management, marketing and production. It does not matter whether a client’s employees are located within one office, or an unlimited number of international offices, we can still bring them together to learn and implement specific business processes collectively. Our approach to global localization enables us to provide clients with a truly international service with that all important personal touch. Appleton Greene corporate training programs can be provided virtually or locally and they are all unique in that they individually focus upon a specific business function. All (CLP) programs are implemented over a sustainable period of time, usually between 1-4 years, incorporating 12-48 monthly workshops and professional support is consistently provided during this time by qualified learning providers and where appropriate, by Accredited Consultants.
Executive summary
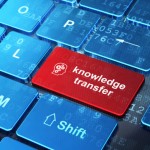
Acquisitive Growth
In today’s context of changing markets, technologies and business models, and in conjunction with historic levels of available capital, acquisitive growth has emerged as an increasingly compelling approach to transformational growth. However, as has been empirically proven growth through acquisitions is fraught with pitfalls and inherently risky. Successfully acquisitive growth requires the confluence of many factors that go beyond the traditional phased steps of a typical process. In my experience success is a function of bringing together the elements of people, processes, and technologies into a set of capabilities that are custom-made for an organization’s particular strengths, circumstances and aspirations. Winning in today’s dynamic markets demands bold, unique and sustainable strategies. The following are the stages of such an approach that I have found to create high probability, profitable growth that stands the test of time.
Additionally, while the M&A industry has many advisors available, they tend not to be operating executives who have lived through all the elements I will lay out below. Many simplistic guidelines exist, however what its clear is that the difference between success and failure with acquisitive growth is not in rote adherence to some set of processes, rather it is found in the combination of process discipline and strong application of experiential, practical knowhow. The nature of this knowhow is to apply and allocate the elements below in a smart, efficient manner to achieve exemplary outcomes for the specific client’s unique situation and circumstances.
Strategy Development: Whether at the corporate level or in a specific business unit, clients would be taken through steps to clarify the markets and segments where they currently compete and where they want to go in the future, what differentiates them from competition, where capabilities need to be refined or built, and the various functional elements (e.g. systems, processes, structures, etc.) critical to sustain profitable growth. Approach would be a combination of review of current strategies/capabilities, interviews and facilitated discussions and structured workshops. Outcomes might be a strategy to bring a particular business into a new growth phase or to meet changing competitive environments, or at the enterprise level might entail “platform building” whereby new businesses, sectors or legs are build from the ground up through foundational initial acquisitions and subsequent organic and inorganic initiatives.
Market Focus: Where will we hunt for acquisition targets? If a company allows too-wide of a scope will find themselves suffering from expensive resource drains/distractions and/or dilute efforts. Therefore, following the alignment of enterprise/business strategies the process will seek to focus the market segments and the business criteria to qualify a company to be elevated to possible target.
Research Possible Targets: Simply put, take the descriptions and criteria from above and create lists of potential targets that might fit. Each such company is researched for available information, any currently available knowledge the client might have, etc. Output is a gross list of possible targets.
Target Approach: Utilizing a number of possible approaches, one that is appropriate for the client is determined. For example, some companies may have business development or sales teams who could participate in this stage, or on the other hand for reasons such as confidentiality, resource scarcity, etc this might need to be put into the hands of specific individuals (senior executives, dedicated M&A executives, 3rd party services, etc.). Each company is different, so this is an exercise of matching needs with capabilities. The objective is to screen the gross target list to elminate those who have “killer facts” such as big contingent liabilities, prohibitive complexity such as a company with a complex ownership structure, our any other aspects that renders a target not acceptable for the next step.
Cultivation: This is a very critical part of the overall process. The essence of this authentic, genuine and meaningful relationship-buidling which requires a combination of individuals with certain skill-sets to ‘sell’ the prospects on being acquired, patience and persistence. I have many approaches, processes and techniques that I have and continue to use to great effect in this regard. Output is a short list of interested targets who have moved to active discussions and in-person meetings.
Target Assessment: During the cultivation phase as it gets more advanced, a critical success factor for effective acquisitive growth is the ability to narrow the list with limited amounts of information. This is important because the next phase is quite intensive so any company can not practically thoroughly assess all such targets. In other words, how does a client gain the insights needed to do this? Some might consider this the ‘phase I due diligence’ whereby, prior to the engagement of expensive resources such as lawyers, accountants, etc., an overview of a target’s current status is determined. Through structured and open discussions, the client engages in discussions with the targets to learn as much as possible..
Preliminary Offer: Structuring of a term sheet or letter of intent based on finding to date. Depending on these findings, certain terms may be included to lay out a) value expectations; b) focus for due diligences and commitment to support it; and c) various legal terms typical for these agreements. This tend to be non-binding agreements meant to establish exclusivity of dealings for a period of time, high level terms that both parties agree to, and confidentiality. Given my background, I have the abilility to craft these documents with minimal legal cost.
Due Diligence: This is yet another element of acquisitions that can take several different forms. Depending on the situation and capabilities of both clients and targets, due diligence activites tend to have different scopes and approaches that match each particular circumstance. A simple example would be a private company target versus a public company. With the latter, sellers often limit potential acquirers to only publicly available information whereas private companies may have limited information at their disposal. Therefore, each approach must be designed for purpose, with the output being a customized plan for a particular target. This leads to both more efficient and cost effective processes as well as deeper insights to help with final decisions.
Deal Making: After the due diligence phase, and with a set of terms already agreed, the negotiations begin to finalized the terms of value, liabilities and the myriad legal and busses considerations that must be addressed and finalized. Whether as chief negotiator or as a trusted advisor to the same, I would bring my experience and talent to bear on this phase as well as some structured approaches/guidelines.
Integration Planning: Concurrent with the commencement of due diligence, full attention is required to determine the structure, resources, plans and teams for post-closing integration. Specific approaches and processes would be employed here to ensure that a proper integration leader is named (critical), robust but prioritized integration plans (e.g. IT and Finance integration might be a first priority for some companies), organizational and assimilation plans, and specific actions in several other area. Among the more difficult and critical elements of integration is culture. While culture is a key consideration in the pre-offer phases, it tends to be among the more challenging aspects to successful acquisitions and an area where experience from a career of hands-on accountability of acquisitions brings valuable insights. Several pro-active approaches can be introduced to the clients to determine which is best to employ with any particular integration.
Execution: From plans to execution requires much more than a roadmap. While such roadmaps are critical, it is the confluence of leadership and human capital, prioritized focused actions to achieve specific results, and finally sustainable integration to bring into the client’s company the full potential of the value creation possible. Tools exist and can be created to provide structure and management support to achieve this consistently.
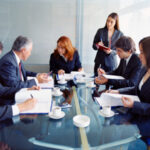
Important And Strategic Elements Of A Growth By Acquisition Approach
This program has thus far concentrated on the role that acquisition strategies play in driving growth.
However, this assumes that the acquisitions are carried out properly on its own. Experience has shown that acquisitions may both produce and destroy value, with the execution of the transaction typically making the difference.
The following are crucial and strategic elements that support successful acquisitions:
• Considering strategic fit: Purchasing merely for the sake of purchasing is little more than management hubris. The target businesses should in some manner meet the needs of the buyer’s company strategy (i.e. product or service line, geographic reach, etc.).
• Addressing culture fit: Due to cultural mismatches between the two merging organizations, some of the largest mergers in history have failed. It is important to take into account a company’s culture because it directly affects how it creates value.
• Doing thorough due diligence: This guarantees that the buyer “looks beneath the hood” of the company they are buying and that the price they are looking to pay for the company reflects its intrinsic value.
• Integration: Even when the share purchase agreement’s ink dries, the deal is not finalized. The two businesses must now start an integration process to ensure that they grow into something greater than the sum of their individual parts.
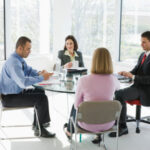
What To Watch Out For During The Entire Acquisition Growth Process
Investigating less evident problems within the target company is the goal of the due diligence procedure.
This ranges from contracts with sizable clients that are about to expire to potential legal proceedings resulting from past business decisions.
But there are a few things that the buyer should watch out for on a more strategic level.
They consist of the following:
• Culture: Even if this phrase keeps coming up, it is crucial to the success of M&As. The culture of the target company should be thoroughly researched by prospective buyers in order to have a sense of what they are getting into.
• Competitive Edge: Is the target company “plain vanilla” or does it engage in any activities that offer it a competitive advantage (which we’ll define as the capacity to produce above-market value over the long term)?
• Leadership: Would the target company’s leadership complement your own leadership team in a positive way? Spend some time with them while conducting your research to see whether this might be the case.
• Possibilities: Are there any prospects that the target firm can take advantage of that your business won’t be able to in the near future? Let’s say it’s because of a service or product line they offer that is expected to see rapid expansion.
• Synergies: Where do your two companies’ synergies lie? Are they really complementary, or does purchasing the target company actually run the danger of causing some of your company’s income streams to be cannibalized?
Program Objectives
The following list represents the Key Program Objectives (KPO) for the Appleton Greene Acquisitive Growth corporate training program.
Acquisitive Growth – Part 1- Year 1
- Part 1 Month 1 Business Assessment – Assessments can be incredibly valuable tools for organizations of all sizes. A comprehensive assessment methodology can help you evaluate your organization across multiple dimensions. But what are business assessments, what do they entail, and what are the benefits? Business assessments can help you identify areas of improvement and potential acquisitive growth. By taking a comprehensive approach, you can get an accurate picture of your organization’s strengths and weaknesses. Assessments can also help you develop actionable plans to improve your business. At their core, business assessments are all about providing clarity. When you’re feeling overwhelmed by the day-to-day details of running a business, it can be difficult to step back and get a clear picture of where your company is headed. That’s where assessments come in. By taking a comprehensive look at your company’s strengths and weaknesses, you can develop a clear road map for success. Assessments are an essential part of any business plan. By evaluating your company’s strengths and weaknesses, you can develop a roadmap for growth. Furthermore, assessments can help identify areas where your company may be at risk. By addressing these risks early on, you can avoid potential problems down the road. In addition, assessments can help you benchmark your company’s performance against others in your industry. This benchmarking process can give you valuable insights into areas where your company may need to improve. Ultimately, regular business assessments are a crucial tool for any organization that is looking to grow and thrive.
- Part 1 Month 2 Strategic Aspiration – A Winning Aspiration defines the purpose of your enterprise, its guiding mission and aspiration, in strategic terms. The first choice of the strategic choice cascade is winning aspirations. Here we ask, “what is our winning aspiration.” Strategically, our winning aspiration defines our purpose. Aspirations are a view of the future. Qualified with “winning,” it is the ideal future that we strive to achieve. Unless you deliberately set out to win, it is impossible to do so. A business that only wants to participate rather than succeed will invariably fall short of making the difficult decisions and large investments necessary to succeed. Aspirations that are too modest rather than lofty are much more harmful. Most businesses fail because they have low expectations.
- Part 1 Month 3 Segment Focus – Every company aspires to grow. But, in a market where competition is fierce, inorganic business growth requires insight and innovation. Segmenting the market and customers is among the most effective techniques to promote acquisitive growth. Yet as numerous businesses have shown, artful segmentation can result in a significant competitive advantage. The purpose of segmentation is to inform your marketing approach. Using this method, it is feasible to recognize and categorize groups of potential clients based on their shared preferences, needs, and interests. This method effectively identifies the demographics most likely to value a specific good or service you provide. Furthermore, it may assist you in positioning that service so that it outperforms that of your rivals.
- Part 1 Month 4 Targeted Offerings – Everything the market offers, be it products or services or any experience, is known as a market offering. Market offerings are also divided among themselves based on the nature of the offering. Read along to understand the role and value of market offerings. Individuals within a market have different wants and needs. As a result, businesses in the market offer various products and services. The ultimate aim of businesses is to fulfill all the varying wants and needs of the population. Providing better target offerings and standing out in the market will eventually lead to more loyal customers and a broader customer base. People expect businesses to add value to their lives in various ways, precisely the purpose of market offerings – satisfying customer needs.
- Part 1 Month 5 Target Pool – The purpose of this workshop is to map out the offerings that one wants to develop or enhance for the focus segments defined by WDP3. A target pool is at the intersection of Targeted Offerings and Focused Segments. For example, if your strategy is focused on growing a currently manufactured product beyond your existing markets, you’ll want to know all the players who make these products in the markets where you don’t currently play but aspire to. In this simple case, the target pool would be derived by researching the current suppliers in these focus segments and profiling them for certain things such as size, channels to market, etc. The approach of this workshop is to take the Targeted Offerings and in a way and ‘map’ them with the Segment Focus areas we developed previously. In reality you might only need to do one or few of these approaches, but the workshop can develop the understanding and skills to do this work, which is in essence synthesizing the ‘strategic play’ associated with any acquisitive growth program.
- Part 1 Month 6 Target Identification – Target identification in acquisitive growth is the process of identifying potential companies or assets that align with the strategic objectives of the acquiring company. It involves conducting comprehensive research, market analysis, and due diligence to evaluate various factors such as financial performance, growth potential, synergies, industry trends, competitive landscape, and cultural fit. The goal is to identify targets that offer strategic value and can contribute to the acquirer’s growth, profitability, market position, or diversification objectives. This process requires careful evaluation, consideration of risks, and alignment with the acquiring company’s overall M&A strategy to ensure successful integration and value creation.
- Part 1 Month 7 Target Approach – All business investors are “financial” investors – the real question is how “strategic” is their ability to leverage the assets of the target. Providing practical guidance on approaching a business target and conducting initial due diligence depends on the investor’s criterion, competencies, and execution bandwidth. At this point, you will have identified a target or group of targets and you are attempting to learn enough about the target to determine whether to proceed with developing a meaningful indication of interest. Of course, an active seller is likely prepared for the sale process and represented by an advisor who is postured to provide the financial and operating information necessary for investors to quickly determine the suitability of a deal (i.e., a pitchbook and defined protocols for communication and information access). However, many desirable targets may not be seeking a sale because business conditions are favorable, and their businesses have been managed to provide options to the owners regarding continued independence and turn-key ownership and management succession. If the former, you, as a prospective buyer may have already pinged on the radar of the seller, and if the later, you have mined for target opportunities and are ready for the next step to accomplish an acquisition.
- Part 1 Month 8 Deal Approach – The M&A landscape is becoming increasingly competitive and the balance of power is shifting further in favour of buyers. For attractive businesses, however, sellers may wish to make divestments through an auction process which is designed to elicit competitive bidding among interested parties to facilitate the sale of a business or stake in a company at the highest price and on the best possible terms. Not all transactions require collaboration between the buyer and the seller, however. In many instances, an auction is still a better approach than a negotiation. The trick is in knowing which process to use when. To make that choice, you need to clearly understand your potential buyers, the characteristics of the asset in question, your own priorities, and the relative importance of speed and transparency to obtaining the best price.
- Part 1 Month 9 Cultivation – (non-auction)
- Part 1 Month 10 Cultivation – (organized process)
- Part 1 Month 11 Confirm Target – Assuming initial contact and conversations go well, the acquirer asks the target company to provide substantial information (current financials, etc.) that will enable the acquirer to further evaluate the target, both as a business on its own and as a suitable acquisition target. After producing several valuation models of the target company, the acquirer should have sufficient information to enable it to construct a reasonable offer; Once the initial offer has been presented, the two companies can negotiate terms in more detail.
- Part 1 Month 12 Talent Assessment – Talent decisions can be made with less precision, discipline, and data but frequently require more complexity than other integration decisions (such as decisions about goods, markets, or customers). M&A leaders must “up their game” in talent assessment if they want to succeed. In the end, the acquirer must decide if current employees from the target (the acquired company) are the most qualified to carry out the goals of the new organization.
Acquisitive Growth – Part 2- Year 2
- Part 2 Month 1 Talent Strategy – There are numerous tactics available for talent acquisition. But not every organization benefits from every method or strategy. When developing your strategy, consider the following factors: industry, size, development trajectory, types of positions, leadership, and more.
- Part 2 Month 2 Integration Strategy – The process of integrating a buyer and seller to the extent required to realize the anticipated benefits from a merger or acquisition is known as an M&A integration. An M&A integration plan outlines the merger’s goals, top priorities, performance indicators, non-negotiables, and scope.Getting agreement among your leaders on the integration strategy is the first stage in an M&A integration. At least two to three months before the deal closes, they should make it clear.
- Part 2 Month 3 Business Plan – Lack of a business strategy before an acquisition is one of the main mistakes that many M&A practitioners make. When considering an M&A, the business strategy is a vital resource. It provides comfort to those funding the deal that the reasoning behind it is sound and that the decision to acquire is not being made on a whim, as well as a roadmap for what you’re looking for in a business acquisition.
- Part 2 Month 4 First 90-Day Plan – HR must be quick and efficient when acquisition is at the core of a company’s growth strategy. The first 90 days are crucial for the organisation’s long-term performance as well as for the retention of individual employees. We can win hearts and minds by day 90 and have a better probability of them becoming productive team members if we have a robust acquisition plan.
- Part 2 Month 5 Valuation – One of the biggest challenges in negotiating a business acquisition is typically price haggling. The intricacy of business valuation makes this more challenging because a fair value cannot be determined without thoroughly examining the company’s financial data, sales trends, customer and supplier base, and many other factors.
- Part 2 Month 6 Synergy Analysis – A significant driver of value in M&A transactions is the potential for establishing synergies. A synergy is the idea that two businesses might be valued more highly when united than when valued separately. Knowing the possible synergies in an M&A transaction is crucial to any agreement, for both the buyer and the seller.
- Part 2 Month 7 Due Diligence (Foundational – Foundational due diligence is an organization’s baseline due diligence requirements that they must have on file for every vendor relationship, regardless of risk level, in order to do business with them. With origins in the private-sector world of business and finance, the term “due diligence” refers to the process through which an investor (or funder) researches an organization’s financial and organizational health to guide an investment (or grantmaking) decision. The decision to fund or not to fund is based upon a balance of objective data analysis, insight into the general state of organizational health and stability, and intuition. A sound and thorough due diligence review is the process through which all the factors that make up that equation are uncovered and understood. It is the process in which a program officer seeks the “truth” about an organization. Foundation program officers are faced with multiple challenges in assessing whether to recommend a grant to their board or decision-making committee. First, they must ascertain whether and to what extent the proposed activity coincides with the foundation’s guidelines and priorities. Next, they must assess the worth of the proposed activity itself — does it advance the fi eld, provide needed services or generate new learning? If the proposal survives this initial scrutiny, it must then be weighed for its relative merits beside many other worthy proposals. This process requires a great deal of skill and sensitivity. Due diligence protects a foundation’s investments and reputation and advances its mission and overall strategy.
- Part 2 Month 8 Due Diligence (Business Plan) – When you receive a proposal on your desk, the first step of proposal review is generally a consideration of the alignment of the applicant organization and proposed project with your foundation’s guidelines and interests. If this initial review is positive, due diligence typically commences with broad research and information gathering to provide a good understanding of the organization, how it fits into the field and the way in which this project will advance your foundation’s strategy. You might also contact colleagues for their view of the organization and its work. Then, you move on to get to know the applicant on a deeper level, including interviews with some combination of the executive director, board chair, other board members and staff members key to the proposed project. Each of these activities is covered in depth in this tool.
- Part 2 Month 9 Deal-Making (Direct Negotiation) – Direct negotiations are a deal making process in which an agency may contact a single contractor of its choice to submit a quote or tender without having first gone through a genuine competitive process.
A variation to an existing contract can also be a direct negotiation. Bargaining between buyer and contractor is a critical element of the process. The objective is to reach agreement on all terms and conditions and to obtain the goods and services at a price that is fair and reasonable to both the contractor and the agency. Direct negotiations are not intended to avoid competition or to discriminate against any organization and must be conducted in a manner consistent with the standards of behavior and requirements. A suitable assessment, based on comprehensive knowledge gained through specific market research, will need to be made to justify direct negotiation. - Part 2 Month 10 Deal-Making (Auctions) – Many (if not most) complex deals between buyers and sellers—from home sales to purchasing auctions to corporate mergers—qualify as auction deal making. Deal making (auctions) give sellers the opportunity to avoid making the difficult tradeoffs of traditional negotiations or auctions— competition versus value creation, for example, or many versus few bidders. In fact, sellers can take the best of both worlds— negotiations and auctions—to ensure they get a great deal. Auction deals have the following features: 1. One-on-one negotiations. At some stage of the deal making process, the seller engages one or more buyers in private discussions about the asset on the table. 2. One or more rounds of bidding. The seller also pits potential buyers against one another in an auction. 3. Several, but not too many, potential buyers. Deal making at auctions need enough parties to spark an auction but not so many that one-on-one negotiation would be difficult for the seller to manage. 4. Process ambiguity. In a traditional auction, the seller determines the process (whether there will be a single round of bidding or multiple rounds, for instance), and buyers are passive participants. In auction deal making, by contrast, the process is up for grabs. Buyers can try to shape the process to their advantage, as in the case of an auction contestant who approaches a seller about negotiating privately to move beyond the single issue of price. In general, whether you are the process setter or a bidder in an auction that has features of a negotiation, don’t assume that the rules are set in stone. Instead, change the game by thinking about how you can influence the rules, parties, and assets to your advantage.
- Part 2 Month 11 Documentation – The paperwork phase of a merger or acquisition is crucial. It might be regarded as the merger and acquisition process’s soul. With due diligence complete, parties make the final decisions on moving forward to execute the transaction. For legal teams, this comes with several responsibilities. Corporate or pre-clearance filings must be made in advance of the closing date. These include merger filings, amendments, ordering of good standings, or issuance of bring-down letters.
- Part 2 Month 12 Communications – An increase in M&A activity indicates a potential deal for entrepreneurs, business owners, and C-suite executives. In the event that a tempting deal is successful, it would be advisable to view an employee communication plan as a crucial component.
Methodology
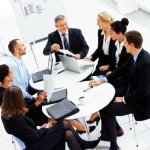
Acquisitive Growth
It’s challenging to make this kind of acquisition successful. Seven fundamental operating principles are used by profitable corporate and financial purchasers, according to research. Almost all phases of the acquisition process, from the selection of candidates through post-merger management, are impacted by these ideas.
• Insist on cutting-edge operating tactics.
• If you can’t identify the leader, don’t make the deal.
• Provide top executives with significant incentives.
• Connect pay to variations in cash flow.
• Accelerate the rate of change.
• Encourage lively interactions between the board, managers, and owners.
• Employ the top acquirers.
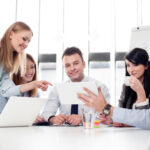
Insist On Cutting-Edge Operating Tactics
High-profile leveraged buyouts like those of Duracell International, Uniroyal, and RJR Nabisco have garnered a lot of attention since the early 1980s. Prices, clever financial arrangements, and bargaining strategies have received a lot of attention. However, the other 2,200+ buyouts that took place during that time period and the fundamental changes in operational procedures that led to profitable outcomes for many of those businesses have received little attention. Although many observers think that LBO enterprises find hidden treasures in the market, more often than not, they only concentrate on enhancing operations.
Two acquisitions, Sunglass Hut International and Snapple Beverage Corporation, show that operating performance—rather than financial leverage, market timing, or industry selection—is the main driver of value creation in successful acquisitions.
Desai Capital focused on accelerating sales growth and developed a new strategy to achieve so when it acquired Sunglass Hut. By acquiring smaller stores in turn and introducing a new store model, Sunglass Hut has expanded from 150 locations to more than 800 since the initial acquisition in 1988. This growth has led to an astounding 37% yearly return. The business introduced a broad product selection rather than depending on two or three popular lines, replaced clerks with limited knowledge of sunglasses with educated customer-service specialists, and implemented a low-cost regional approach.
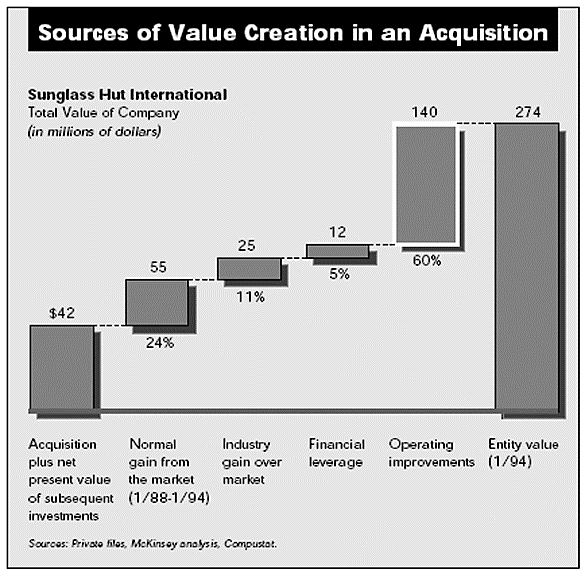
Another illustration of operating improvements is the 1992 purchase of Snapple by renowned financial acquirer Thomas H. Lee Company. Snapple launched an aggressive growth strategy based on quick global expansion and product range extensions shortly after the takeover. The business immediately established its production and distribution network since it anticipated that rivals will soon release their own natural teas and fruit juices. It entered into contractual agreements with bottling and distribution businesses that had excess production capacity, allowing it to launch its product one year before major rivals like Fruitopia (from the Minute Maid division of Coca-Cola Company) and achieve a competitive advantage.
As the Snapple case demonstrates, innovative operating methods help acquirers succeed in fiercely competitive markets like the American food and beverage sector. The takeaway: Don’t limit your search for success to high-growing industries.